The standard setup
The standard ignition system used by the Alfa boxer engine in
the twin carburettor Sprint, AlfaSud and 33 is an electronic Bosch unit, which uses a part
mechanical distributor with a hall effect reluctor trigger, and a conventional coil.
Inputs to it are: +12 volts switched
supply from ignition switch
trigger sensing connection from distributor
The coil also has +12 volts supplied to it, and a low tension
connection from the electronic ignition box. In addition, it outputs a signal to the
Tachometer on the drivers instrument panel. This wire is green with a yellow tracer on it,
and is common with the low tension connection.
A standard HT king lead then feeds the centre of the
conventional distributor cap, and a conventional rotor arm then feeds the spark voltage to
the individual HT leads. The rotor arm is fitted with a spring loaded moveable contact,
which acts as a centrifugally operated rev limiter.
The advance curve of the distributor is pre-set, and only
vacuum advance adjustment is available.
There is not much that can be done with the standard ignition
system, and for most intents and purposes it functions very well. As with any ignition
system, the key is to ensure that all the components are kept in good condition. I have
found that this setup is susceptible to deterioration of the leads, and to spark deposits
on the contacts inside the distributor cap. Beyond this, it is a trouble free system.
It may be necessary, however, to consider the use of harder
plugs if you have seriously uprated your engine. The best way to determine the need for
this is to see what performs best on a rolling road session.
Alternative ignition systems
In order to best deal with tuning the ignition system, an
understanding of what it needs to do is useful.
Why do we need the spark? Quite obviously, unlike a diesel,
the petrol and air mix in the cylinder needs something to initiate combustion. But just
igniting the mix is not sufficient. If you ignite the spark too early, the burning mix in
the cylinder tries to stop the piston on the compression stroke, rather than pushing the
piston dow on its power stroke. If it is far too early, it will ignite the mixture as it
is coming into the cylinder with the valve open. If it is a little too late, the burning
mix is chasing the piston down the bore, rather than pushing it, again wasting power. This
leads to overheating and burnt valves.
So why not just have the distributor fire at a set point?
Well, that would work perfectly if the engine was kept at a constant speed and constant
throttle setting. The trouble is, the mix will burn at a certain rate, and as the engine
speeds up, the mix has to either burn faster, or more practically, you need to start
burning it earlier. That forms the beginning of the advance curve. So all you have to do
is have some centrifugal weights that change the advance as the engine speeds up, right?
Well, no, not quite. If the cylinder is full of a good mix of
air and fuel, like when the throttle is wide open, it will burn nice and quickly when
ignited. If the cylinder only has a little air and fuel, like when the throttle is closed,
the mix burns slowly. So a means is needed to advance the ignition even more when the
throttle is closed and cylinder filling is not so good. This can be compensated by
something that senses when the throttle is closed. The vacuum advance capsule does this,
as vacuum exists in the inlet manifold when the throttle is closed, but reduces as the
throttle is opened. In addition, the vacuum acts a a free mechanical force to pull the
distributor mechanism to more advance against a spring.
So, the standard distributor comes with a centrifugal advance,
and an additional vacuum advance mechanism. By repeated testing, and using different
springs and weights, a distributor is modified to produce a curve that similar to the
ideal that an engine wants to see. The manufacturers are then able to be certain that for
a given engine and specification, their curve will be satisfactory for all engines
produced to that specification.
The mechanical curve is fairly linear, as are
the advance requirements charecteristics of production standard engines. Unfortunately,
lumpy cams and improved breathing characteristics change what advance is required.
The trouble is that speed and load are not the only factors
influencing the ignition timing requirements. A weak mixture burns slower. A higher
compression ratio makes the mix burn faster, and vice versa. Higher temperatures also make
the mix burn faster. Certain conditions will cause pre-ignition.
Look at what a lumpy cam does. Due to the
increased overlap, at low speeds, some of the air and fuel that goes into the cylinder
goes out of the exhaust valve, some of the exhaust gas pushes the intake mix back up the
inlet tract, and if running carburettors the low speed fuel mix can be considerably off
the ideal. The result of this is that the effective compression ratio is very low, you may
have a poor fuel to air ratio, and the quality of the charge in the cylinder is
contaminated by exhaust gas, which does not want to burn. You therefore need considerably
more advance so that the mix has ample time to light off. Unfortunately, you have stepped
on the throttle to accelerate, so you have reduced the vacuum advance. Poor running
characteristics at low speed are therefore made even worse.
Why not just set the distributor to give more
advance? Well, as your engine accelerates, and climbs onto the cam, suddenly everything
starts working wonderfully. Remember that compression ration increase to make the cams
work? That means that you need less advance. The valve overlap that previously was
spoiling the intake charge is now helping to pull more air and fuel into the engine,
increasing the volumetric efficiency of the cylinder and increasing the effective
compression ratio even more. The carbs are on song now, so the mix is good quality.
Everything is saying 'less advance'.
Combine the need for more advance at low
speeds and less at high, and it can be seen that a steeper curve is needed, which can be
altered by changing the spring rates inside the distributor. In the good old days before
electronics, these requirements where met by companies like Aldon, who modified
distributors to achieve this. This worked to a degree. The trouble is that our lumpy cams
and mods have not finished giving us trouble yet.
All of the mechanical advance mechanisms
assume one thing; a more or less linear change in ignition requirements. Unfortunately,
our tuned engine is nothing but. Different engine speeds make different things work. At
2500 rpm, the engine may be off cam, with lots of pulse and resonant effects doing their
damnedest to spoil the quality and quantity of the intake charge. You need lots of
advance. At 3000 rpm, the engine comes on cam, and all those pulse effects are stuffing
tons of air and fuel into the cylinder. You need less advance. At 3500, a pulse length, or
resonant effect suddenly starts working against the flow (you would see this as a dip, or
flat spot in the power curve - very common on modified engines). You suddenly need more
advance again. In addition is the possibility for pre-ignition at high load, which
requires backing off the advance.There is no easy way for a mechanical distributor to do
this.
Depending on the budget available, or the need, it is possible
to introduce a completely different setup that completely gets around this. This is a
distributorless fully electronic solid state system.
The advantage of this system is that you are
always going to have the spark occurring at exactly the moment that the engine wants to
see it, regardless of the type of cam, exhaust, fuel system etc. A mechanical distributor
follows a pre-set curve which is determined by springs and centrifugal weights, with
correction for low load by means of a vecuum connection. It is crude, but for a production
engine works well enough because the manufacturer tailored the particular weights and
spring rates for a standard of engine. The advance curve is a compromise, but a closely
matched one. For a modified engine though, that compromised curve is not going to be as
well matched, simply because you have altered the requirements of the engine.
A fully electronic system can be set to give
the spark at exactly the right moment whatever the engine whatever the conditions.
This setup comprises the following components:
Twin double ended coil unit
Electronic Control Unit
Water temperature sensor
Air temperature sensor
Throttle position sensor
Crank angle / position sensor
Crank speed sensor
The coil unit is a solid state unit comprising two parallel
coils, each with two outputs. When triggered, each coil outputs two sparks. By connecting
these coils to plugs in the cylinders which are at top dead centre at the same time, the
cylinder on the firing stroke is ignited, and the cylinder on the exhaust stroke simply
wastes the spark generated. This is the wasted spark principle.
As a result of this setup, each coil must be individually
triggered, and the timing of this is controlled by an electronic 'brain'.
The 'brain' is a mappable elecronic control unit (such as the
Emerald M3D ECU, as I used on my 16v), which can also control the injection. This takes
inputs from the sensors listed above. The crank sensor enables the ECU to determine
at which angle the crankshaft is at, and at what speed. Using these inputs, the ECU is
then able to look at RPM, throttle demand, water temperature and air temperature to
calculate exactly what the correct advance is. It does this by looking at a three
dimensional 'map', which plots advance against throttle load and RPM. Additional
correction factors for temperature and cold start requirements are then superimposed on
these values.
Once the ECU has determined
when the spark is required, it then triggers the appropriate coil. The coils are connected
directly to the spark plugs, so no HT king lead or distributor is required. It is a simple
system to physically install.
The 'map' referred to earlier is one
which is determined by actually running the engine on a dynamometer, either an engine
dyno, or more frequently a rolling road. During this, the engine is run at different
speeds and loads, and the exact ignition advance is set by changing the timing until the
engine is giving the best power. The system can also be changed to sort out dips in the
power curve, prevent pre-ignition, pulse tuning effects, off cam running etc. In addition,
it can be used to auto stabilise idle running, and act as a soft-cut and hard cut rev
limiter.
Other benefits of this are:
it can easily be reprogrammed to suit
further mods to your engine, or transferred to another engine
There are no moving parts to
wear, or lose adjustment
I decided to fit a fully solid state
electronic ignition system to my 16v.
Physically installing the
distributorless system
The assumption is that you are fitting this equipment to a 16v
engine. For 8v engines please refer to footnotes.
Please refer to the fuel
system section for installation of the ECU.
What you will require are
A suitable Electronic Control Unit
(ECU). I chose the Emerald M3D unit
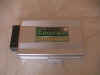
The Emerald M3D ECU
A dual double-ended coil ignition pack, probably from a Mondeo or Escort zetec engine
(mine was a 1800 MkV escort 16v unit). REMEMBER to get a piece of the wiring loom complete
with connector!! Ford does not sell this separately.
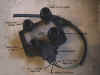
the Zetec coil unit
A three way male/female electrical
connector
Either 4 off No1 cylinder plug leads from a 1991 1800 Escort, or a pack of plug lead
adapters (a photo of these is below)
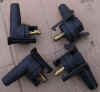
the Zetec coil adapters required for the
HT leads
You will also need to supply a
switched +12 volt supply and some wire to connect the ECU to the coil.
The zetec double ended coil is fitted so that at the same time as cylinder no 1 is firing
on its firing stroke, the spark plug for cylinder no 2 will be firing on its exhaust
stroke, and ditto for cylinders 3 and 4. Before anyone writes to me to tell me that it
should be 1 and 4, and 2 and 3, remember that the boxer has an unusual firing order of
1-3-2-4, rather than the normal 1-3-4-2.
The +12v line is connected to the
centre wire of the coil connection. The ECU pin for the no.1 cylinder is connected to the
wire on the side of the coil connector marked 1 and 4, and the remaining ignition coil ECU
pin is connected to the remaining coil wire.
A separate feed goes to the
tachometer, but you can connect the green/yellow tacho wire from the existing system
direct to the ECU tacho output. It works fine with the standard tacho fitted to the car.
The ECU will automatically sense the
crank position from the crank sensor, so you do not have to worry about setting the timing
in the conventional sense. Once the car is running, it will be adjusted using the PC
software.
Oh, by the way, when you remove the distributor, remember to blank off the hole!
That's the theory, now does it
work....?
After all this is the interesting
task of trying to get the car to at least fire up.
Once all this injection and distributor-less ignition
hardware had been fitted, I had to try to make it all work together. I attempted to use
the instructions that come with the EMS to get the engine running.
The EMS came programmed with a basic, safe fuel and
ignition map from a similar sort of engine, perhaps from a 1.6 or 1.8 ford Zetec. The
engine did not want to run using this, point blank. After many hours of trying, I decided
to take a step back and simplify the system in order to attempt to diagnose why it
wouldn't run.
I had previously stated that I might run into
problems, and that as a contingency I could stick on the carbs and the distributor. Well,
that proved to be my saviour, or at least some of it did. I could not very easily stick
the carbs on because it would mean a change of fuel pump, plus devising a means of
attaching the throttle pot to the carbs. The distributor, however, could simply be bolted
back into place, and the connections remade by re-attaching the spade connectors.
This I did, and with the help of a can of 'Easy
Start' and the lap top, we tried again. Squirting the Easy Start in while cranking showed
that the engine wanted to run. By richening the mixture VERY considerably, it finally
burst into life. It seems that the fuel required by the engine was considerably more than
he engine was getting using this map and fuel pressure.
However, once I had the fuel mapping at a point where
the engine was happier, I attempted to refit the distributorless system. The engine would
now run, but was a pig to start, and it was obvious that my crank sensor was not helping.
It seems that the output signal from the sensor was not very strong at low speeds (below
1000 rpm), and the ECU was not able to consistently read from it. As a result, the speed
site information was switching between 0 and site 2, with the result that the injection
and ignition was being switched on and off. This results in an erratic idle and poor
running characteristics at low speed.
The ECU sensitivity can be increased to compensate
for this, but will have to be done at Emerald in London, at the same time as the rolling
road mapping is performed. As an interim measure, the distributor ignition has been
refitted and the car currently runs using this.
Notes
Just a few comments regarding general ignition
related issues.
Firstly, spark plugs; the ones fitted are the Golden Lodge
multiple electrode type. I have used both these and standard electrode plugs on Alfa Boxer
engines with absolutely no apparent difference in
the way the engine runs. Any comments or findings from anyone who has some experience of
different plugs in 16v engines would be appreciated.
Secondly, the plugs on a 16v are a bastard to get at.
No ifs, no buts, they are buried well into the heads, and the chassis rail stops you
getting full access to them. They are impossible to see with the engine in the car without
the use of a mirror. Getting the plug leads on and off them is also a thankless task. The
rears are even worse than the fronts, and the fronts are pigs. My recommendation is to
change or check the plugs at every opportunity that the engine is out or dropped down.
You will need to devise some fiendishly clever bit of
tooling to get them out, just in case you need to. I used a Halfords plug socket, plus a 3
inch long extension bar and a slimline ratchet or tommy bar. This was satisfactory, but I
will be making a purpose built tool as access to the rear plugs is difficult even with
this.
If you are fitting all this kit to an 8v engine, you will need
to install either a 36 - 1 or a 60 - 2 toothed wheel for a crankshaft trigger sensor.
You will have to fit a water temperature sensor, although this
is easy as both inlet manifolds are tapped to accept sensors. Just fit a 16v sensor in the
manifold with the blanking plug.
If keeping carburettors, a throttle potentiometer will be
required. Fitting kits exist, and are easily available. |